Coroplast: On the Path to High Performance
The digital transformation is forcing companies to change how they think. That applies even to a successful automotive supplier like Coroplast, a family-run company that specializes in electrical wires and harnesses along with the technical adhesive tapes to protect them. With its high-voltage wiring that will be used in electric cars, the company has laid a superb foundation for future sales. But Natalie Mekelburger, who became Chairwoman of the Board of Management in 2006, believes she still needs to encourage change—because new competitors are entering the market and unit volumes per order are likely to decline.
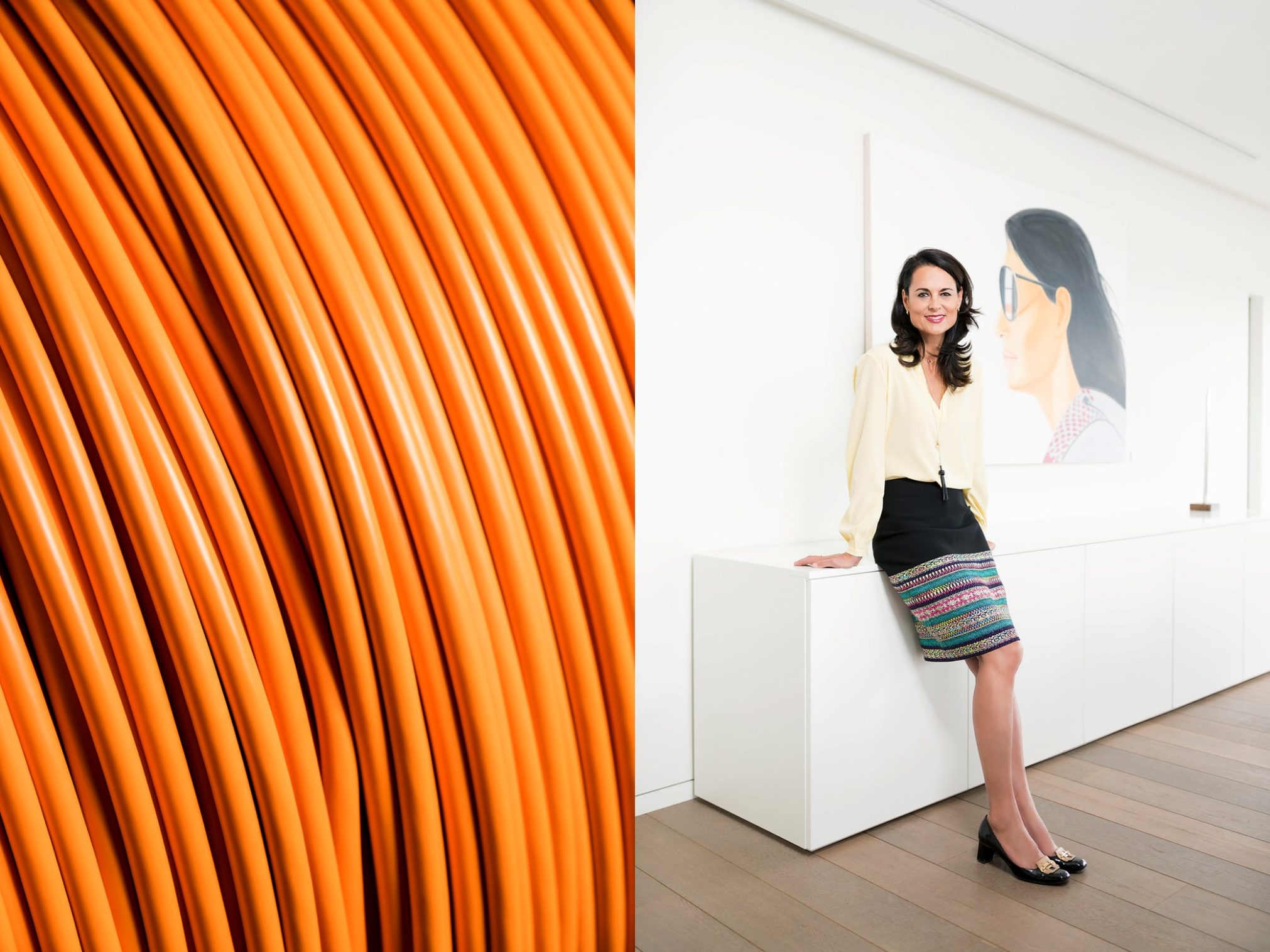
The new structure will increase our flexibility, enhance our ability to innovate, and intensify customer relationships.
Day-to-day operations at Coroplast are highly technical and digital—but for Natalie Mekelburger, culture is an essential part of the company. “Work should be a place not only of exertion but also of inspiration,” she says. Which is why she promotes modern art and has installed a spacious lounge with a fireplace, terrace, and sofas on the top floor of company headquarters, which is open to all employees. “We think freely and openly here,” she says. Success bears her out.
The project with Porsche Consulting
Natalie Mekelburger worked with Porsche Consulting to create a new structure. Three core business units are now run by a holding company. “As much decentralization as possible, as much centralization as necessary” was the guiding principle.
A digital agenda was also worked out with the help of Porsche Consulting. It calls for transforming production into a smart factory and digitalizing work flows. “In five years we will be a paperless company,” she says. “That is the vision we are pursuing.”
Making Culinary Waves
Food preparation on the Anthem of the Seas, one of the world’s largest cruise liners, is not only about taste and pleasure, but also about communication, precision, and performance. The nearly 5,000 guests want superb cuisine, so the forty-two chefs require flawless operations. Royal Caribbean Cruises commissioned Porsche Consulting to help optimize the processes below deck and behind the scenes. Automotive production served as a model in many instances. For example, the first plate to receive its final garnish is the first to leave the galley—to be served quickly in the best quality to the guest.

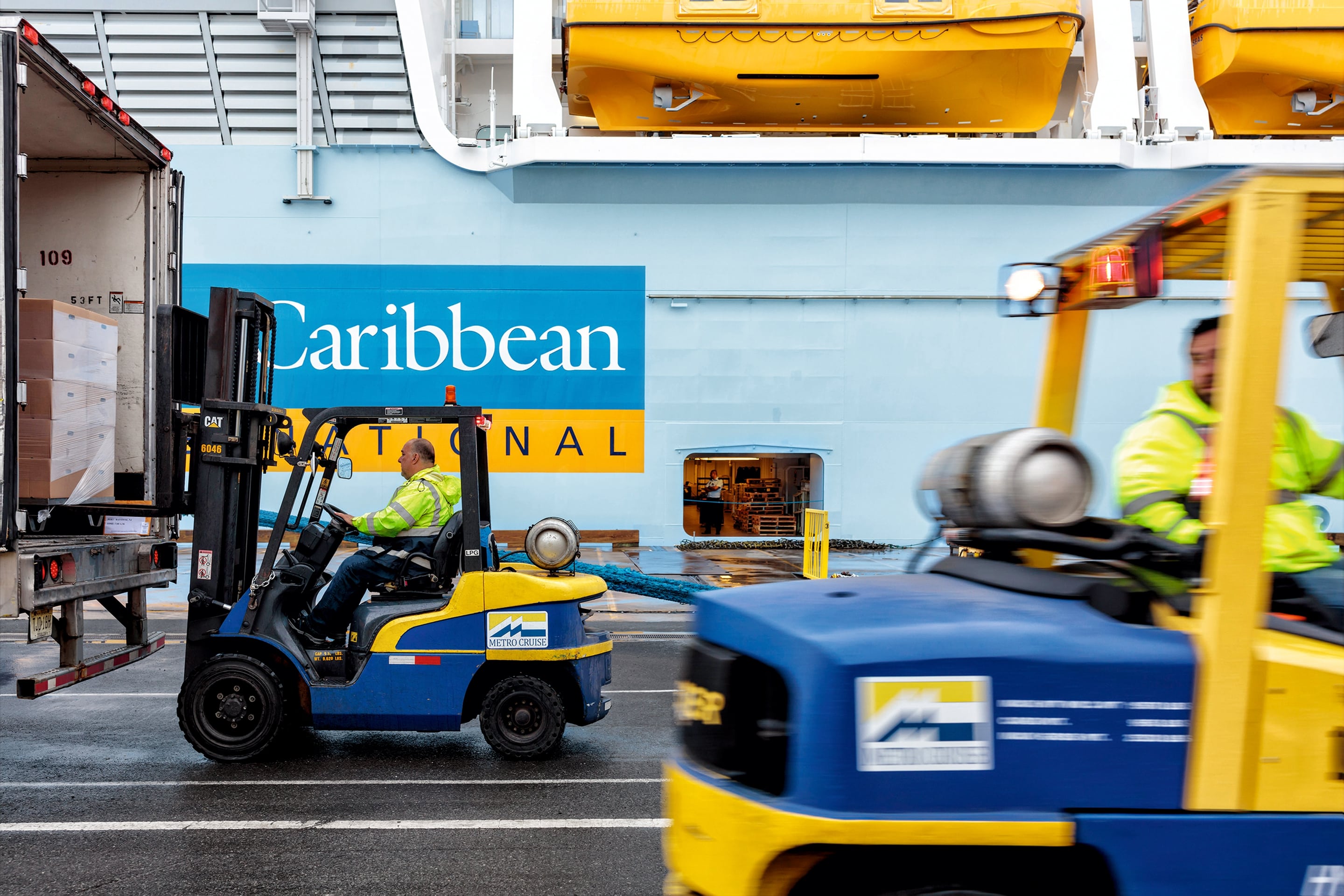
“Guest satisfaction went through the roof. We are so much more efficient—far beyond what I would ever have expected.”

