Smart Factory Production Reloaded
Classic conveyor belts? They won’t be found in the factories of the future. Their place will be taken by autonomous transport systems and assembly stations for efficient, flexible, and sustainable production.
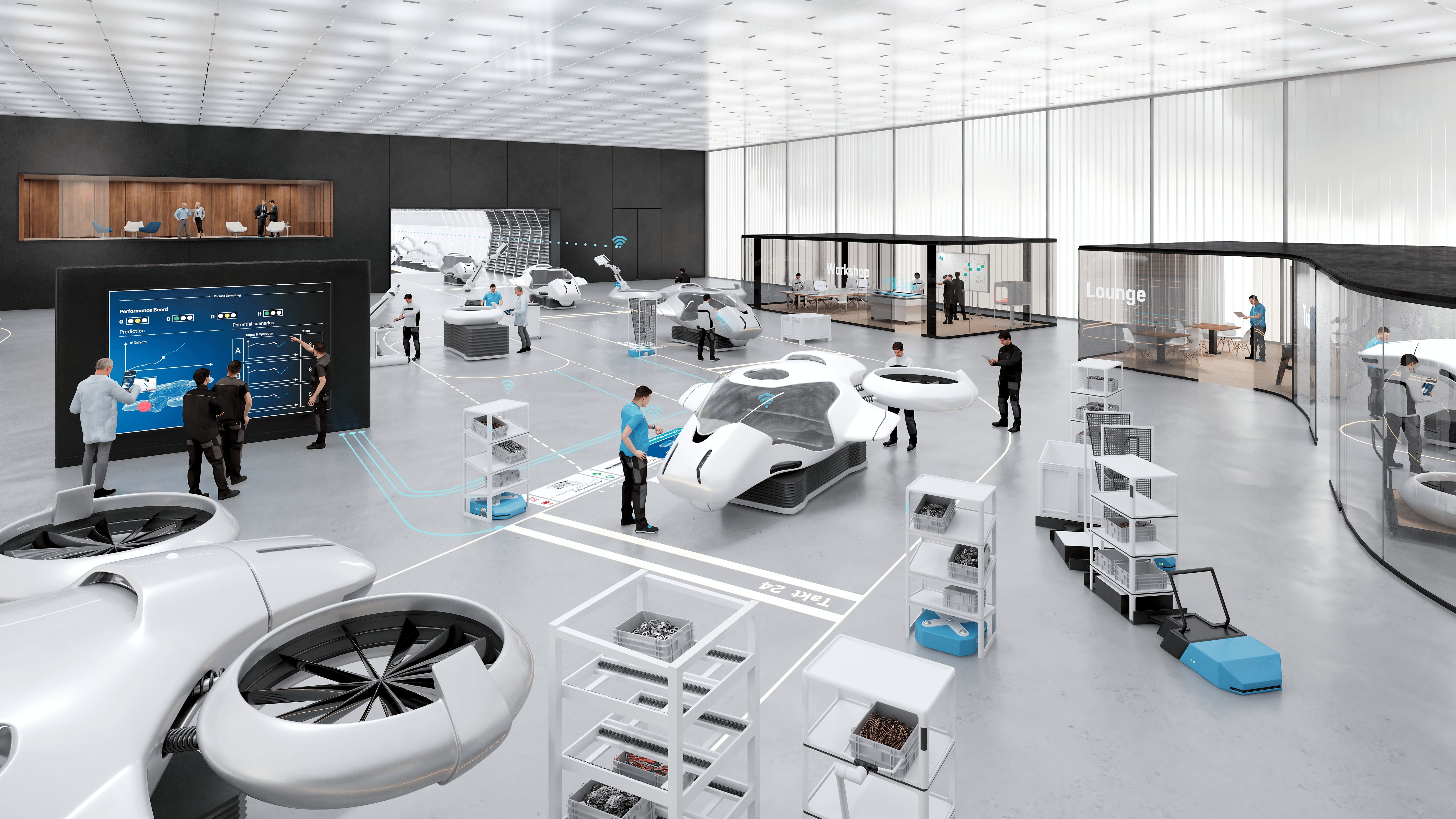
Checklist for Smart Entrepreneurs
The advantages of a smart factory are obvious. But companies need to change course to get there. These are the requirements they should meet in order to reach their destination.
01.
We have communicated a specific vision to all our employees and quantified the goals of a smart factory.
If digitalization is not precisely defined, it can elicit vague fears. But a clear and understandable vision, for example in the form of an image, promotes acceptance and encourages employees to participate actively in the transformation.
02.
We have assigned responsibilities and equipped teams with the requisite freedoms and budgets.
A smart factory needs movers and shakers. That doesn’t mean it’s imperative to appoint a chief digital officer. But it is important for specific employees to be released from other duties for key projects, together with decisional powers and a separate budget for innovations.
03.
We are familiar with key technologies and therefore also know what skills we need to develop.
An ecosystem with external partners is a crucial factor in success. But it is just as important to be as independent as possible when it comes to key technologies. Internal expertise should be developed early on and in targeted ways by means of both training and hiring.
04.
Our smart-factory projects are connected and can be easily scaled up and transferred.
Pilot projects and minimum viable products quickly generate important insights. To extend them beyond isolated applications in order to facilitate success on a company-wide basis, contexts and connections need to be considered right from the start. An adaptable IT structure makes it easier to transfer processes to other areas.
05.
Our employees are open to new ideas and put innovative projects into practice on a transdepartmental basis.
A company’s culture can be the greatest obstacle to transformation, but also its greatest accelerator. Hackathons and in-house fairs can instill enthusiasm in employees for change. Cross-functional teams are an antidote to silo mentalities.
How ABB Makes Future Factories Flexible
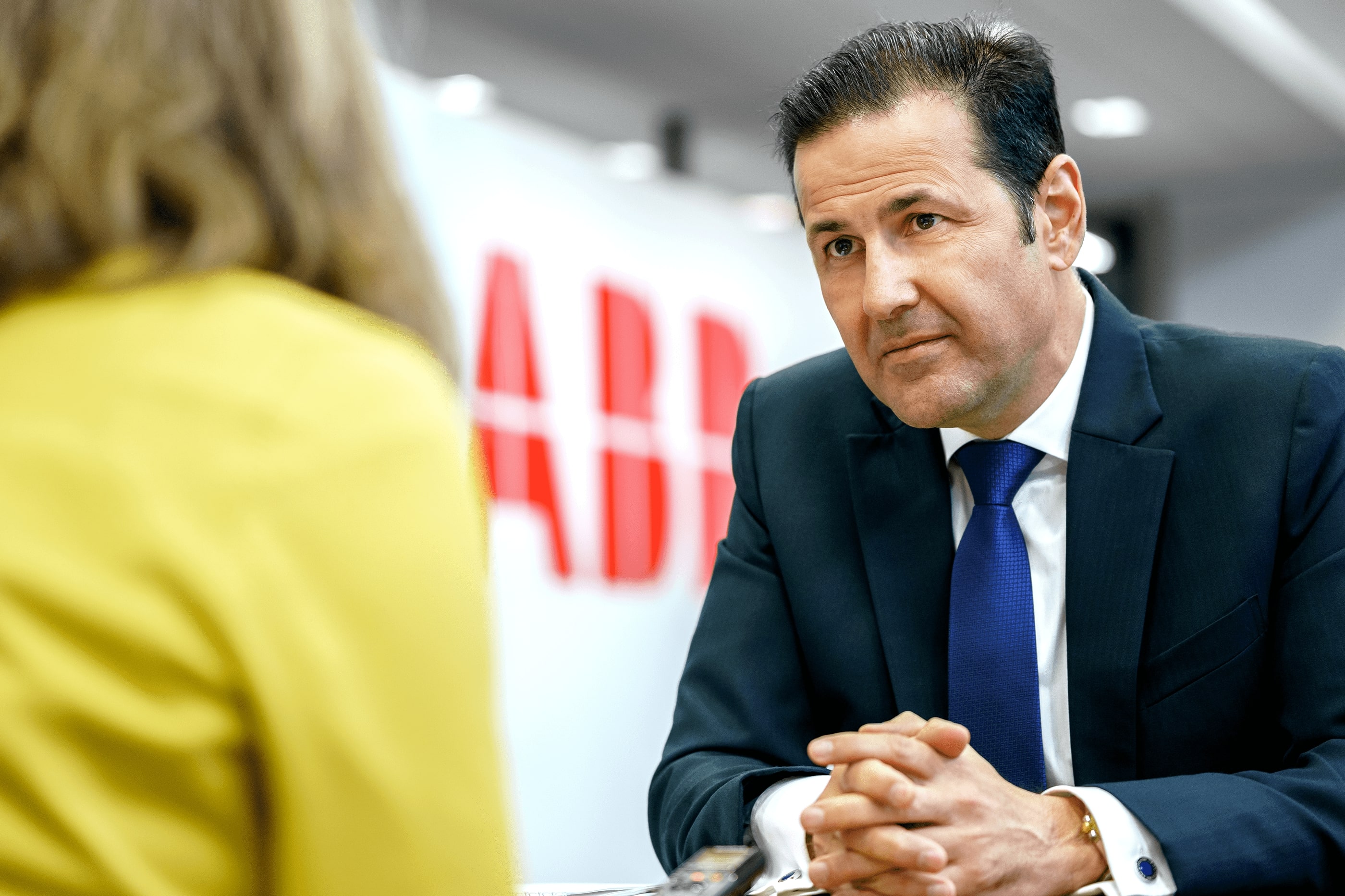
Mass production and customized manufacturing—the ABB international industrial group seeks to unite these apparent opposites with the help of automation and digital technology. This Swiss company that began making generators 130 years ago now makes machinery for highly automated and flexible factories. Demand is high, because consumers want individual products, faster delivery, and low prices, says Javier Rodriguez, Vice President of Strategy for Robotics at ABB. Above all, demand is changing so quickly that manufacturers of this size can no longer make secure plans. Factories will therefore have to adapt their products and production levels themselves to market conditions in the shortest possible periods of time. Artificial intelligence is expected to help. What paths should the automated guided vehicles take between assembly stations? How fast should the robots work? Algorithms will be making these decisions in the flexible factories of the future.
The project with Porsche Consulting
ABB’s fully automated, flexible factory near Shanghai will start operating in late 2020. Robots will be built by robots there. The highly automated system will decide on its own, without human control, whether to speed up
or slow down production and whether to shut down or start up assembly islands. Porsche Consulting supported the manufacturer in designing the IT architecture, defining digital use cases, and identifying potential savings.